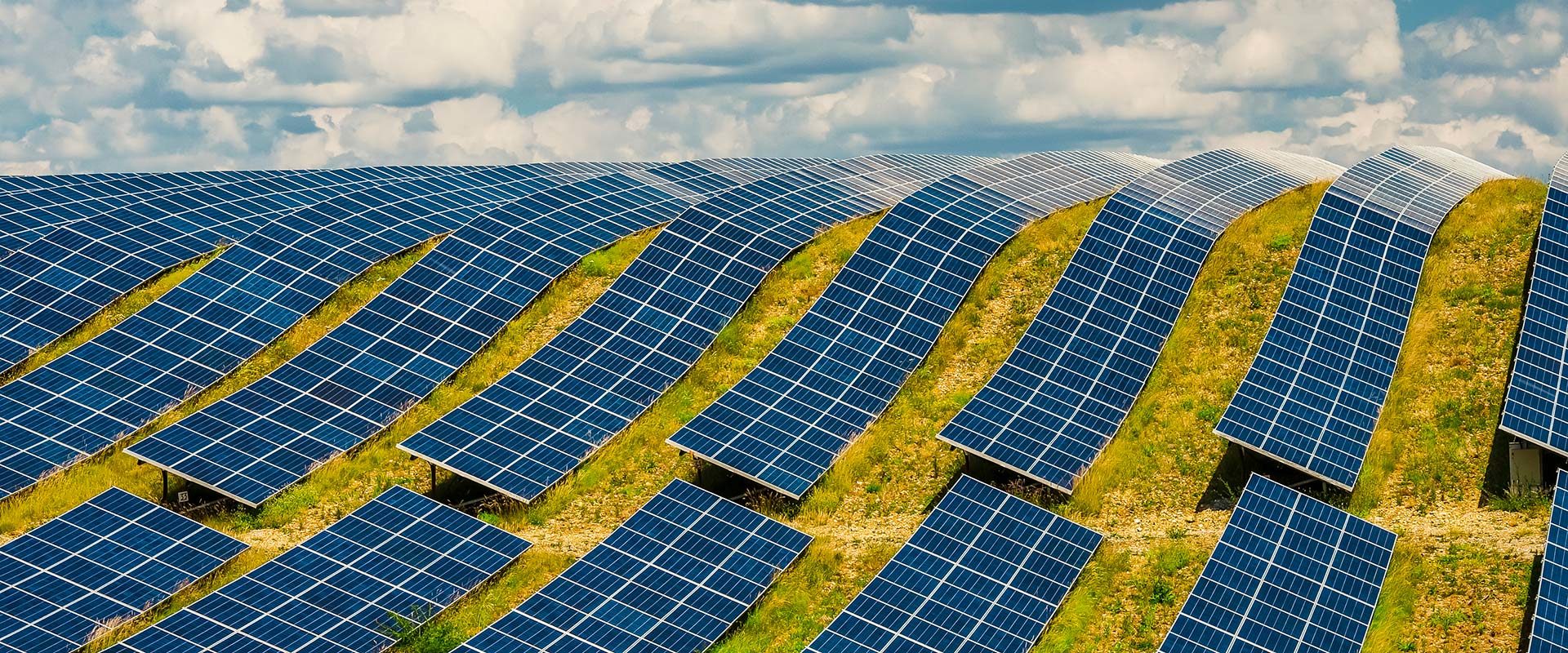
Utility-Scale Services
Protect your solar investment with Schneider Electric’s worldwide network.
We offer services in over 110 countries providing 6,000 Solar experts in all regions / time zones. From spare parts replacement to long-term power plant services, our experts provide continuous high-level support in order to ensure the optimum performance of your PV plants.
The Schneider Electric global footprint in all countries makes us a truly global company with local knowledge and footprint.
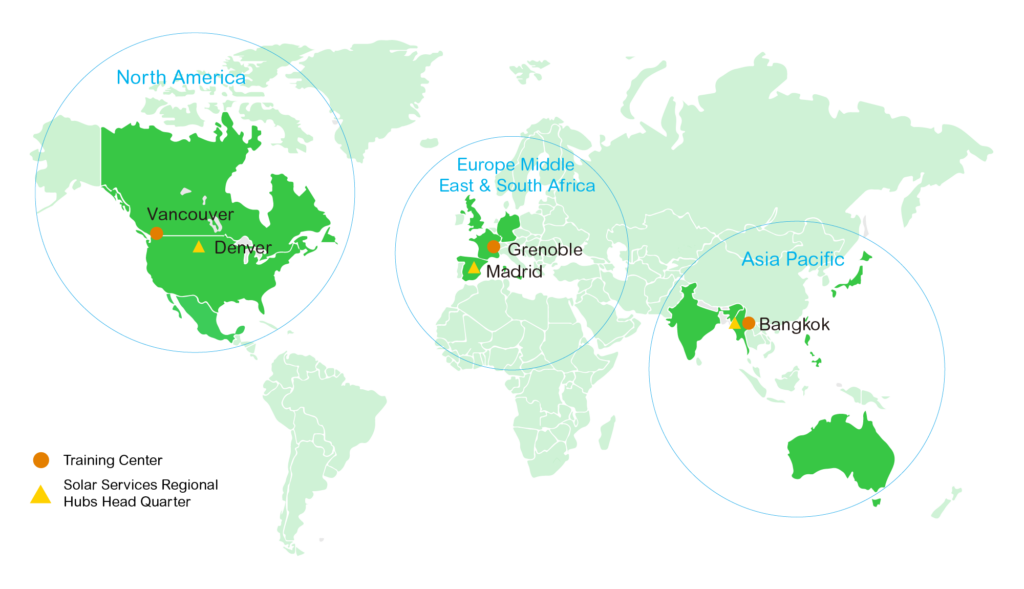
Regional hub benefits
The Regional Hub is accountable for:
- 24/7 hotline with L1 / L2 services operation specialists
- Scheduler and dispatchers
- Dedicated field service engineers
- Dedicated control room
- Single point of contact for spare parts
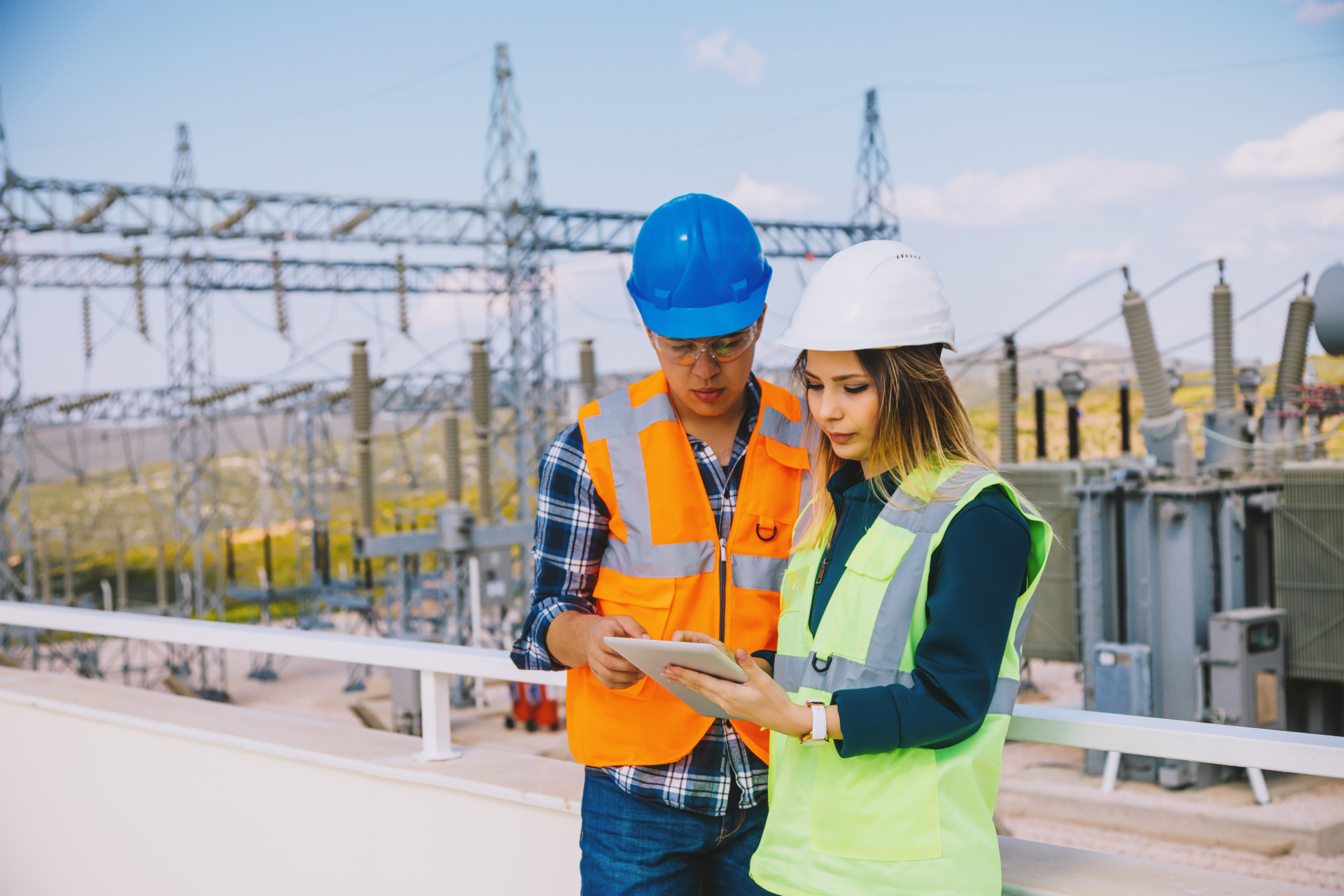
Why partner with Schneider Electric Solar Business?
- Our solutions are designed for fast, easy and efficient servicing
- We have adapted our footprint to better attend to your needs
- Minimize your total cost of ownership with our service offers
- Advanced analytics capabilities to reduce component failures

Digital Services
We bring intelligence to day-to-day operations through our monitoring platforms and our ability to optimize the performance of your Power Plant.
Conext™ Viewer is the local and remote user interface for Conext SmartGen™ power system. It is used to monitor and configure the inverters on site and remotely. It also provides advanced features for troubleshooting.
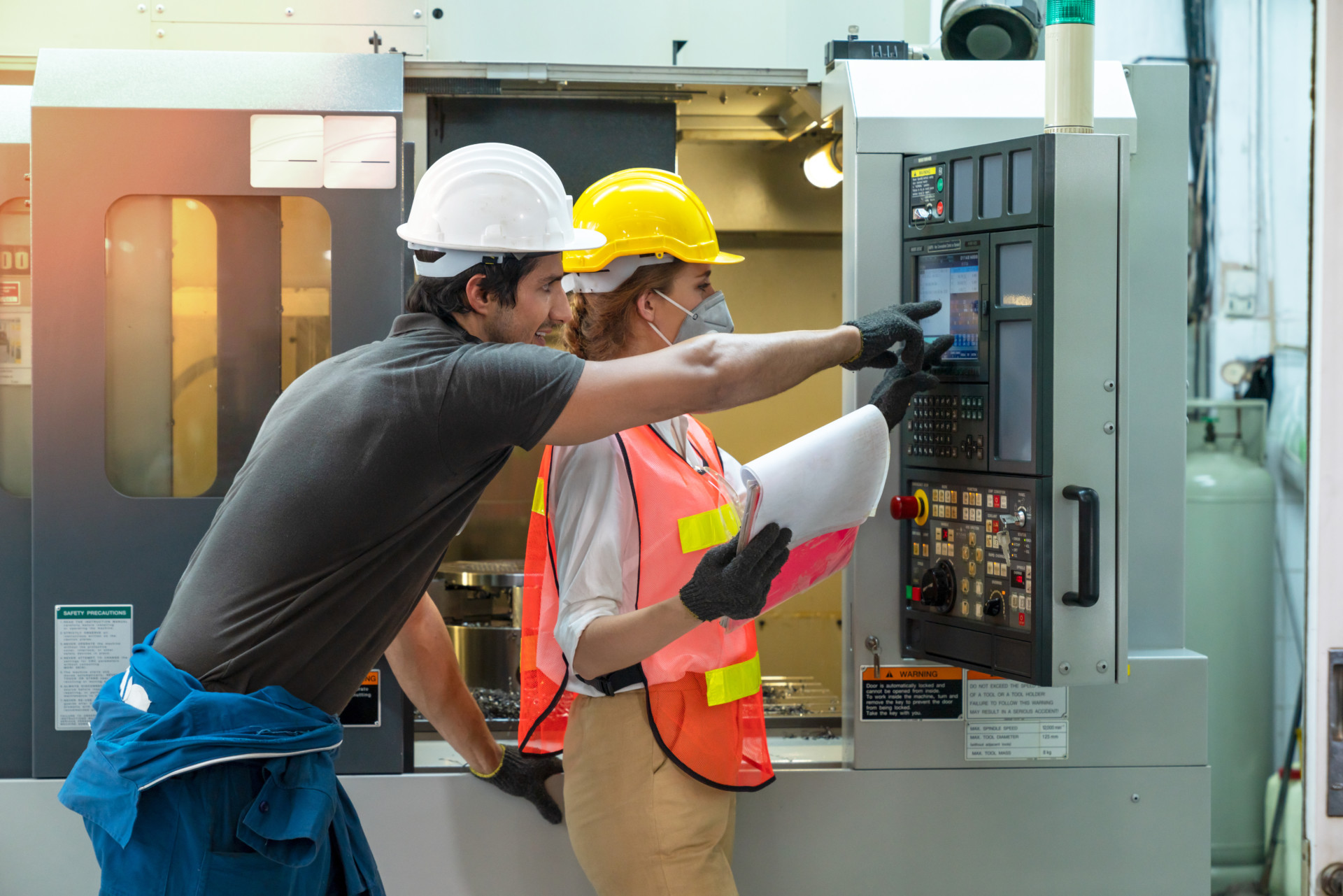
Power Plant Services
Our worldwide footprint is designed to optimize the logistics flow and supply chain efficiency.
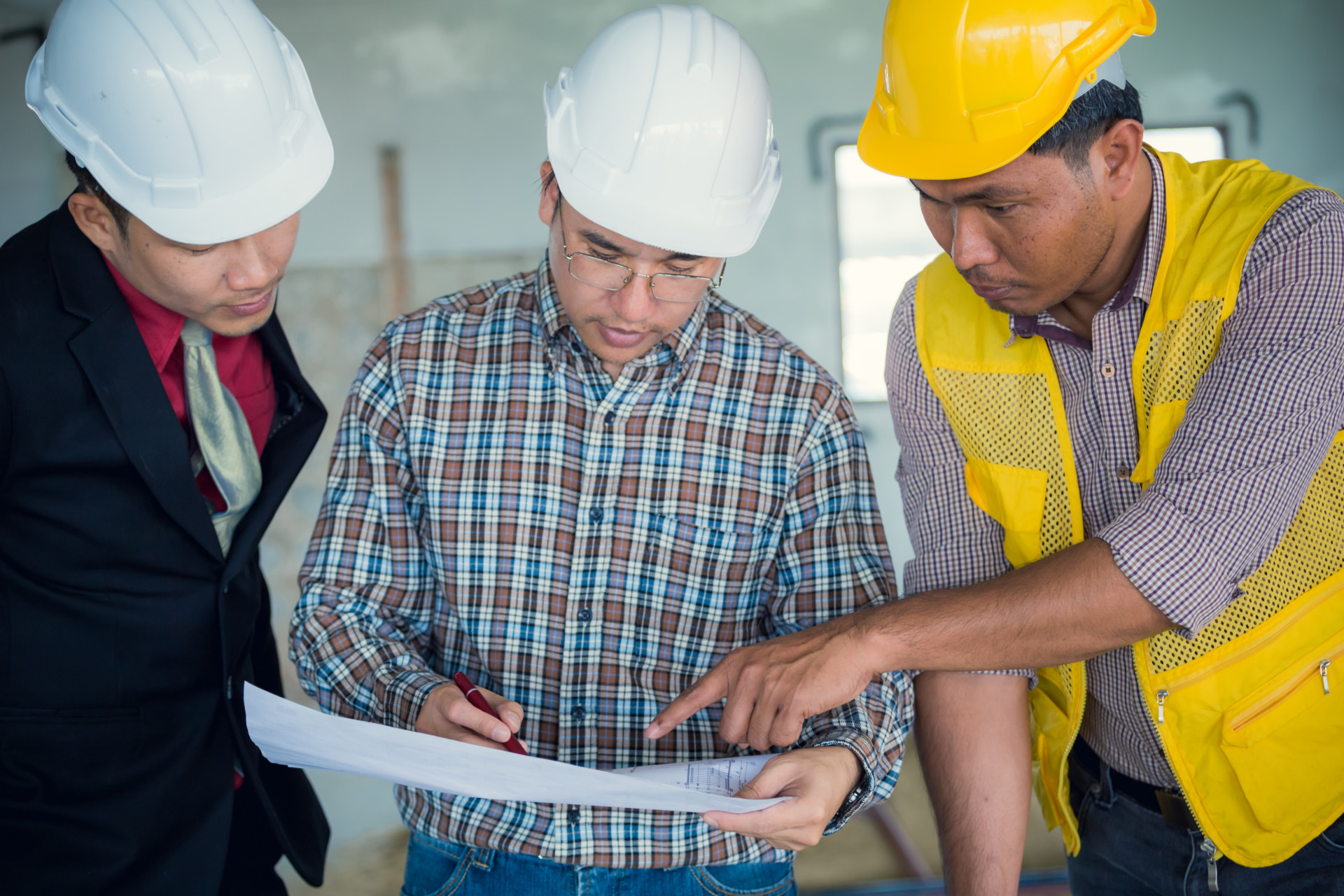
Spare Parts Management
Long-term contracts to secure and sustain your assets throughout their lifecycle or on-demand to match specific needs.
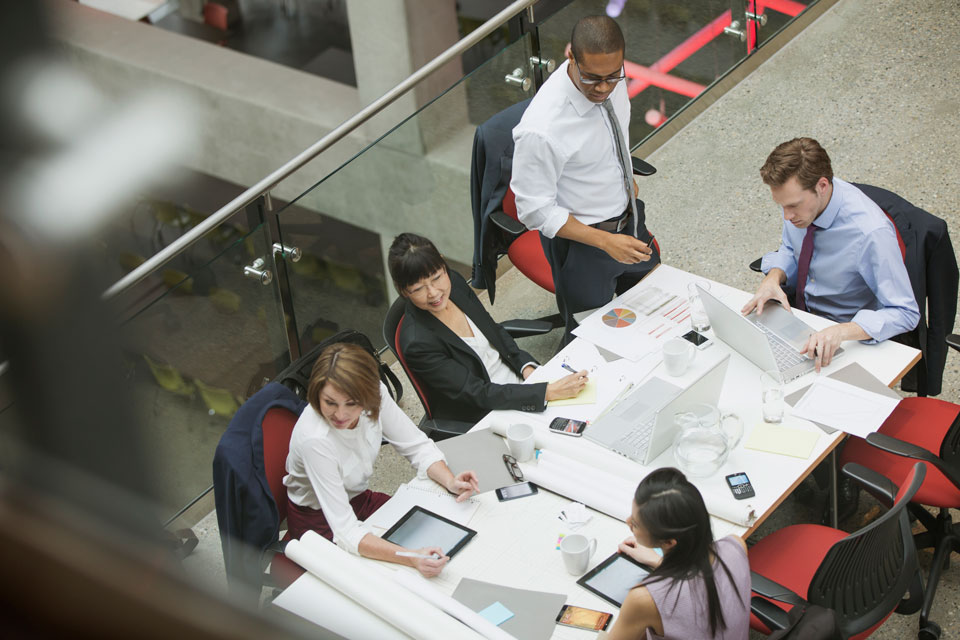
Schneider University
Benefit from tailor-made courses in one of our training centers.